Prolog
Am 30 August 1970 musterte ich von der M/S „Westfalen“ in Antwerpen ab. Es war der Wunsch meines alten Arbeitgebers Otto Stinnes, noch bis zum Ende des Monats eine Urlaubsvertretung als Leitender Ingenieur auszuführen. Als ich am 1. September 1970 bei Krupp-Atlas meinen Dienst antrat, hatte ich noch immer kein Dienstzeugnis von der Reederei Stinnes erhalten, um es bei meinem neuen Arbeitgeber vorzulegen. Da man mich unbedingt als Betriebsingenieur haben wollte, gab man sich mit dieser Situation zufrieden.
Seit meiner Lehrzeit von 1953 bis –1956 hatte sich einiges verändert. Ein Besitzerwechsel fand statt. Aus finanziellen Gründen musste Hugo Stinnes jr. den Betrieb veräußern. Zuerst kaufte es der Finanzmakler Münemann und 1965 Friedrich Krupp. Die Belegschaft wurde von damals 1600 auf ca. 1000 reduziert. Die Produktpalette hatte sich geändert und der Umbruch sollte weitergehen. Es wurde zum Beispiel die fast neue Gießerei geschlossen und bei der zu Atlas gehörenden MaK in Kiel wieder aufgebaut. Die Atlas-Elektronik einschließlich Mess- und Analysentechnik wurde ausgegliedert, blieb aber als einziges Unternehmen in Bremen und hat bis heute überlebt. Der Schiffbau wurde aufgegeben und viele weltweit bekannte und äußerst zuverlässige Produktsparten verkauft.
Bei meinem Dienstantritt gab es nur noch drei Produkte:
Steinpressen, Seewasserentsalzungsanlagen sowie Wärmetauscher und Behälterbau für Kraftwerke. Ach ja, ich hätte fast die Klarsichtfenster vergessen.
Der Zustand der Werksanlagen hatte sich allerdings so gut wie nicht verändert.
Mein Job als Betriebsingenieur umfasste folgendes Aufgabengebiet:
Wartung, Instandhaltung und Modernisierung aller Bereiche. Es handelte sich um Bürogebäude, Fertigungshallen einschließlich deren Werkzeugmaschinen, Energieversorgung, Fuhrpark, Feuerwehr, Sanitäter und Pförtner, Ausschreibungen für Neu- und/oder Umbauten und Beschaffung der dazugehörigen Materialien. Man nannte diesen Bereich kurz: „Hilfsbetriebe“.
Wie schon zu meiner Seefahrtzeit verschaffte ich mir erst ein mal einen detaillierten Überblick vom Istzustand meines zukünftigen Arbeitsbereiches. Ein in meinen Augen sehr guter Mitarbeiter mit hervorragender Ortskenntnis aus meiner Abteilung begleitete mich. Teilweise standen mir die Haare zu Berge, als ich die tatsächlichen Zustände sah. Bei der Betriebsbegehung während meines Vorstellungstermins wurden mir nur die intakten Bereiche gezeigt und ich hatte keine Möglichkeit, hinter die Fassaden zu sehen.
Hier ein Beispiel von vielen: Im neu errichteten Kesselhaus standen drei schwerölbefeuerte Kessel mit einem Betriebsdruck von 16 bar, leider waren sie nicht für den wachfreien Betrieb konzipiert. Der Dampf diente überwiegend zum Heizen, zur Warmwasserbereitung sowie für Probeläufe und Versuchszwecke für gefertigte Produkte. Auch einige Bürogebäude wurden dampfbeheizt. Jetzt kommt das Unglaubliche. Der Druck von 16 bar wurde von einem Schlosser durch ein einziges handbetätigtes Ventil auf ca. 1 bar reduziert. Es gab weder ein Sicherheitsventil noch andere Schutzeinrichtungen. Jeder hatte Zugang zu diesem Raum. Es ist kaum vorstellbar, wenn ein Unbefugter das
“Regelventil“verstellt hätte. Die Heizkörper in den Bürogebäuden wären geplatzt. Natürlich wurde die Heizung umgehend auf Warmwasser umgestellt.
Es gehörte auch zu meinen Aufgaben, die Gemeinschaftskosten zu senken. Damit verbunden war auch der Personalabbau. Die aufwendige Aufbereitung der werksseitigen Wasserversorgung aus eigenen Brunnen wurde automatisiert. Zwei vollautomatische Rotationskompressoren für die Druckluftversorgung wurden gegen uralte, liegende Kolbenkompressoren ausgetauscht und im Kesselhaus installiert. Die mit Karbid betriebene Azetylen-Anlage wurde stillgelegt und durch Flaschenbatterien, die auch am Kesselhaus platziert wurden, ersetzt. Desweiteren wurde der Flüssigsauerstoff- und Flüssigpropangastank in unmittelbarer Nähe des Kesselhauses umgesetzt. Nach und nach wurden alle Bürogebäude auf Warmwasserheizung und die Werkshallen vereinzelt mit modernen effizienteren dampfbeheizten Heizlüftern umgerüstet. So konnte ich die ersten Mitarbeiter freisetzen bzw. in andere Bereiche umsetzen.
So einfach wie beschrieben war es aber nicht. Ich sollte modernisieren, musste aber um jeden Pfennig bei der Geschäftsleitung kämpfen und das dauerte! Erschwert wurde die Umsetzung meiner Ideen durch stetige und widersinnige Umgestaltung der Fertigungsabläufe, mal zentralisiert und mal dezentralisiert. Hier wurde das meiste Geld zum Fenster heraus geschmissen, denn neue Fundamente für die großen Werkzeugmaschinen kosteten richtig viel Geld. Die Fluktuation der Fertigungsleiter machte dieses Chaos möglich.
Für mich war es eine bittere Erfahrung, nicht mehr selbst entscheiden zu können, so wie ich es als Chief bei der Seefahrt gewöhnt war. Ich musste vieles - sehr vieles - – dazulernen, insbesondere was meine Bauabteilung betraf. Es mussten Hallendächer repariert und Gerüste aufgestellt werden. Bei Umbauten von Gebäudeteilen kam mein Vorarbeiter zu mir und sagte: „Wir brauchen Mauersteine für soundsoviel Quadratmeter einer halb steinschen Wand, Baustahlmatten Q188 und 8m³ Beton 220. Da hab ich erst einmal ganz dumm gefragt: „Was ist das denn?“
Im Winter sah ich auf den Straßen des Betriebsgeländes vielerorts Dampfschwaden aus dem Boden treten. Es handelte sich teilweise noch um Relikte aus dem letzten Krieg. Schächte, in denen die Leitungen verlegt waren, wurden mit Schutt verfüllt. Meistens wurden nur Notreparaturen durchgeführt und in den seltensten Fällen wurden neue Schächte angelegt. Aufgrund dieser Umstände war es auch nicht verwunderlich, dass im Kesselhaus nur ein Bruchteil des Kondensates - Kondensat ist die verflüssigte Form vom Dampf –- zurückkam. So musste stets mit teuren Chemikalien aufbereitetes Stadtwasser zugeführt werden. Unser selbst gefördertes Brunnenwasser war für die Kessel ungeeignet.
Eine brisante Entdeckung
Eines Tages führte mich mal wieder die Suche nach dem Verlauf von alten Rohrleitungen in die Katakomben der alten Waschräume mit den großen ovalen Waschtischen und einer Vielzahl von Wasserhähnen, – an die ich mich aus meiner Lehrzeit noch recht gut erinnerte. Hier lag noch immer der eigenartige Geruch von Schweiß und Kernseife gepaart mit hoher Luftfeuchtigkeit und verbrauchter Luft. Die Rohrleitungen verschwanden in den Betonwänden der Gewölbe. Verschweißte Stahltüren verwehrten mir den Zugang. Ich ließ die Türen öffnen, um den weiteren Verlauf der Leitungen zu erkunden. Beim Begehen dieser Räumlichkeit merkte ich, dass es sich hier um einen alten Luftschutzbunker gehandelt haben muss. Zu meinem großen Erstaunen lagen hier in den heruntergefallenen Teilen von Decken und Wänden im tiefen Staub eine Unzahl von Erkennungsmarken ehemaliger Zwangsarbeiter. Die Namen ließen auf Ausländer schließen. Ein Vordringen in die Räumlichkeiten war leider nicht möglich. Mein Begleiter und ich machten uns Orientierungsskizzen mit Längenangaben, um diese später auf maßstabsgetreue Werkspläne zu übertragen. Bei uns reifte die Idee, von einer anderen Stelle in die Katakomben zu gelangen.
Zu jener Zeit hatten wir es fast täglich mit Anschlagsdrohungen der Baader-Meinhoff-Bande bzw. RAF zu tun. Es musste zusätzliches Überwachungspersonal – insbesondere des Nachts und an Wochenenden – auf der Wasserseite des Betriebsgeländes postiert werden. Bei einer eingehenden Kontrolle der Kaimauer entdeckten wir einen kleinen verdeckten Schacht. Zu meiner großen Überraschung musste dieser in die Richtung der Katakomben mit den Waschräumen führen. Einer meiner Mitarbeiter sicherte mich ab, als ich mich in den schmalen Schacht zwängte. Was ich jetzt zu sehen bekam versetzte mich doch in einiges Erstaunen. Hier lagen von der feuchten Witterung unleserliche Briefe, die mit Briefmarken des 3. Reiches versehen waren, im Dreck herum. Die zuständigen Herren und der Betriebsrat wollten von dieser Sache nichts wissen. Es erinnerte mich an die drei Affen: "Nichts sagen - nichts sehen - nichts hören".
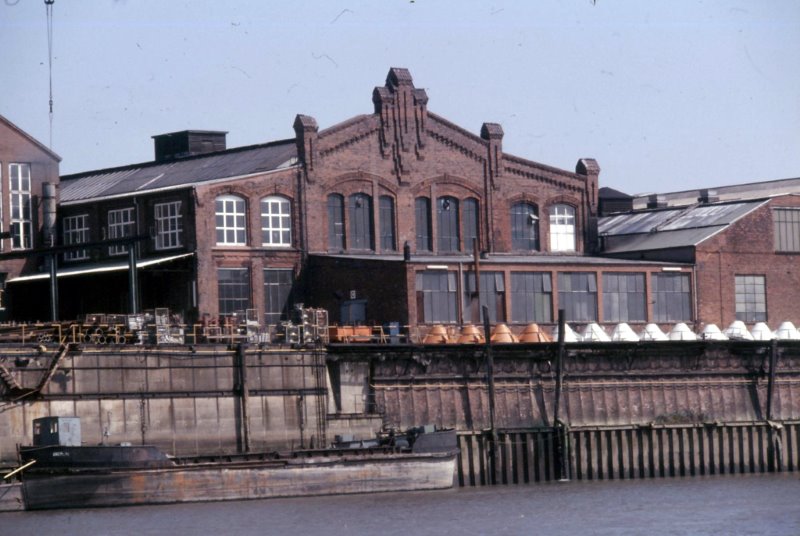
Mit freundlicher Genehmigung durch: Bodo Wenz, Bremen
Auf der Weserseite der Atlas-Werke entdeckten wir den kleinen Einstieg
|
Juli 1971- Urlaub
Während meines ersten Urlaubs machte ich, wie mit dem Betriebsrat und meinem direkten Vorgesetzten quasi per Handschlag vereinbart, meine erste Vertretungsreise als Chief auf der M/S „Boitwardersand“ der Reederei Meyer, Brake von Antwerpen über Panama und San Lorenzo in Honduras. Ich war pünktlich zurück und somit war alles OK.

Bildquelle: photoship.co.uk
M/S "Boitwardersand"
|
Reederei-Union Meyer, Brake
Flagge: Deutschland
Bauwerft: Brand, Oldenburg
Baunummer; 182
Frachtschiff
Tragfähigkeit: 1898 gt
1 Deutz-Diesel mit 1471 kW
Geschwindigkeit: 12,5 Knoten
IMO: 6829848
Reiseverlauf
|

Solvey-Antwerpen/Belgien
|

Panama-Kanal
|

San Lorenzo/Honduras
|

Rückflug: Honduras- USA - Deutschland
|
Allerdings hatte die Rückreise noch einen bitteren Beigeschmack. Der Kapitän hatte es - aus welchen Beweggründen auch immer - nicht für nötig gehalten, rechtzeitig für meine Ablösung zu sorgen. In San Lorenzo, einem kleinen Nest am Pazifik, entschloss ich mich dann, mit dem Lotsen das Schiff zu verlassen. Der Agent brachte mich zur Hauptstadt Tegucigalpa. Hier nahm ich mir ein Hotel und versuchte, kurzfristig einen Flug nach Deutschland zu buchen, aber erst für eine Woche später waren noch Plätze frei. Ich musste es so akzeptieren, zumal ich noch rechtzeitig zum Arbeitsbeginn in Bremen sein würde.
Der Flug begann pünktlich, aber in San Pedro de Sula mussten wir außerfahrplanmäßig landen. Die vollbesetzte Maschine, ein 4-propelliger Flieger, wurde hier nochmals vor dem Weiterflug nach New Orleans gecheckt. Alle Passagiere mussten das Flugzeug verlassen. Dreimal konnten wir einsteigen und mussten dann doch wieder raus. Beim Überflug des Golf von Mexiko war mir nich ganz wohl. Wir erreichten jedoch die USA ohne weitere Probleme. Der Flug nach New York begann ohne große Wartezeit. In New York wurde ich jedoch von der Immigration per Handschellen vom nationalen zum internationalen Flughafen gebracht. Ich hatte ja kein Visum, aber Seefahrtsbuch und Reisepass. Rechtzeitig erreichte ich über Frankfurt Bremen. Allerdings dauerte es ein paar Monate, bis ich meine von mir verauslagten Reisekosten von der Reederei zurückerstattet bekam.
Info: Warum Urlaubsvertretung?
Mein Verdienst bei Krupp-Atlas betrug etwa 60% von dem eines Leitenden Ingenieurs bei der Seefahrt. Hinzu kam, dass bei der Seefahrt Kost und Logis umsonst waren. Ferner profitierte ich als Chief von den monatlichen RP-Geldern und den üppigen Tantiemen der Reederei. Außerdem hatte ich mir ein Haus gekauft, welches noch abbezahlt werden musste. Bei der Seefahrt benötigte ich keinen PKW, den ich jetzt auch noch kaufen und unterhalten musste.
November 1972 - Orkan
Am 13.11.1972 tobte der wohl bis dahin schwerste Orkan seit Beginn der Wetteraufzeichnungen in Bremen. Die höchste Windstärke wurde um 09:30 mit 156 Km/h gemessen. Der Luftdruck erreichte um 09:30 einen Wert von 956 hpa, was für Bremen ein neuer Rekordtiefstwert war. Allein in Bremen starben 4 Menschen. Der Sachschaden ging in die Millionen.
Der Sturm hinterließ auch bei Atlas seine Spuren. Abgedeckte Dächer, beschädigte zum Versand fertige Anlagen. Meine Leute hatten Tage bzw. Wochen damit zu tun, die Schäden an dem Werksgelände zu beheben.
|
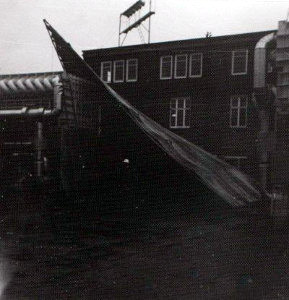
Werftgebäude
|
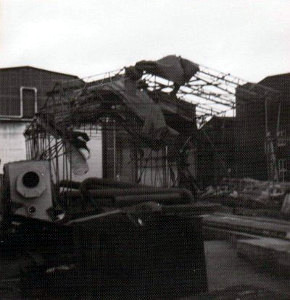
provisorische Halle
|
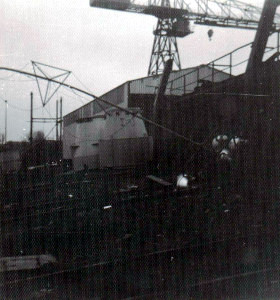
ehemaliger Schiffbauhelling
|
Dezember 1972 - Urlaub
Eine weitere Urlaubsvertretung war auf der „Maria C“ vom 20. Dezember 1972 bis 28. Januar 1973
angesagt.
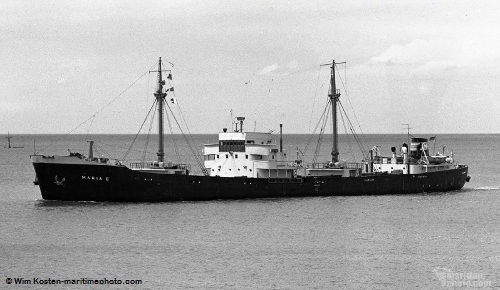
with kindly permission of Wim Kosten dd 15. 09. 2013
M/S "Maria C"
|
Reederei H.F. Cordes, Hamburg
betreut von Carolina Shipping Company, Famagusta/Zypern
Flagge: Zypern
Bauwerft: Turku Yard, Turku/Finland
Frachtschiff
Baujahr: 1942
BRT: 3228
Tragfähigkeit: 5030 tdw
Länge: 98,60,00 m
Breite: 13,82 m
1 ehemaliger U-Boot-Diesel mit 1200 PS
Geschwindigkeit: 9,5 Knoten
Besatzung: 22 Mann
Unterscheidungssignal: P3QA4
IMO: 5133424
Reiseverlauf
|

Schleuse-Brunsbüttel/Deutschland
|

Visby/Gotland/Schweden
|

Ventspils/Lettland
|

Schleuse-Kiel-Holtenau/Deutschland
|
Sanitäre Anlagen
Die sanitären Anlagen der Arbeiter stammten noch aus der Zeit, als ich von 1953 bis 1956 meine Lehre machte. In der mechanischen Werkstatt wurde der erste neue, zeitgerecht ausgestattete Waschraum mit Toiletten errichtet. Er wurde aus den Katakomben in den luftigen 1. Stock verlegt. Als nach ca. drei Monaten die sanitären Einrichtungen aussahen, als hätte dort 'ne Bombe eingeschlagen, traf mich fast der Schlag. Nach der ersten Renovierung machte ich dem Betriebsrat den Vorschlag, oben an der Wand für jeden sichtbar folgenden Hinweis anzubringen: Letzte Renovierung am..... …! Nein, das wollte der Betriebsrat nicht und es dauerte nicht lange und die sanitären Einrichtungen befanden sich erneut in einem katastrophalen Zustand. Abmontierte Toilettenbrillen und -papierhalter etc. In den Slums der dritten Welt, in denen ich während meiner Seefahrtzeit auch war, sah es nicht so aus. Außerdem konnte es keiner auf irgendwelche Ausländer schieben, denn die gab es fast nicht. Auch das war Krupp-Atlas.
November/Dezember 1973 Ölkrise
In der Bundesrepublik Deutschland wurde als direkte Reaktion auf die Krise viermal ein Sonntagsfahrverbot im November (erstmals 25. November 1973) und Dezember 1973 verhängt sowie neue Geschwindigkeitsbegrenzungen eingeführt. Ich war von dem Fahrverbot befreit, da ich im Notfall von zu Hause sofort zum Betrieb fahren musste.
Die Ölkrise hinterließ auch bei Atlas deutliche Spuren. Die Temperaturen wurden in den Büroräumen sowie auch in den Werkhallen heruntergefahren. An den Wochenenden – Sonnabend und Sonntag – wurde nicht geheizt. Erst am Montagmorgen gegen 04.00 Uhr wurden die Kessel hochgefahren. Natürlich waren die Bürogebäude zum Arbeitsbeginn noch nicht wieder durchgewärmt. Die Beschwerden, die bei mir eingingen, waren anormal, da alle wussten, dass gespart werden musste. Hier habe ich mich immer wieder über eine kurz vor der Rente stehende Sekretärin eines Betriebsleiters amüsiert. Sie war immer die erste, die sich bei mir beschwerte. Wenn ich dann zu ihr sagte: „Frau „X,“ es dauert noch einige Zeit bis es durchgewärmt ist“, bekam ich von der alten Dame immer den gleichen Anschnauzer: „ Herr Sander, ich habe ihnen doch schon so oft gesagt, ich bin Fräulein und nicht Frau“! Sie gehörte mit 50-jähriger Betriebszugehörigkeit - wie viele andere auch - zum Inventar der Firma.
Außerdem machte die Ölkrise die Relikte der letzten Jahre –seit Kriegsende – so richtig sichtbar. Die hohen Hallen mit ihren unisolierten und meist nur Halbsteinmauerwerk, die dünnen, hölzernen Hallendächer und die großen undichten Tore hatte man nach dem Krieg nur provisorisch hergerichtet und seitdem nichts mehr verbessert. Es war kaum möglich, mit den uralten Heizlüftern die Hallen zu heizen. Meist waren die elektrischen Ventilatoren defekt. Ferner fehlten vielfach die Kondensatableiter. Der größte Teil des Kondensates versickerte durch defekte Rohrleitungen irgendwo im Erdreich. Die einstigen Rohrleitungsschächte waren zusammengebrochen und mit Erdreich verfüllt worden. Insbesondere die Werkhallen hätten aufwendig saniert oder noch besser abgerissen und nach dem neuesten Stand der Technik sowie den jetzigen Bedürfnissen der Fertigungsprodukte angepasst und ersetzt werden müssen.
Dezember 1973 „Arbeitssicherheitsgesetz“
Im Dezember 1973 wurde in der BRD das neue
„Arbeitssicherheitsgesetz“ verabschiedet. Die Sicherheit, insbesondere die des Menschen, war schon immer mein ganz besonderes Anliegen, so wie ich es früher bei der Seefahrt praktiziert hatte. Hier sah ich in der Zukunft meine Chance.
Bei Atlas, wo dieser Posten noch nicht besetzt war, bewarb ich mich als Sicherheitsingenieur. Diese freie Stelle wurde mir zugesagt, ich musste allerdings noch einen 4-wöchigen Lehrgang bei der Bundesanstalt für Arbeitsschutz und Unfallforschung (BAU) absolvieren.
Urlaub Dezember 1973/Januar 1974
Die letzte Urlaubsvertretung während meiner Zeit bei Atlas war auf der M/S „Andrea“ der Reederei Hugo Bartels in Hamburg vom 12. Dezember 1973 bis 13. Januar 1974. Die Reise war in Charter für die Deutsche Afrika Linie - vormals Woermann Linie - von Hamburg nach Abidjan/Elfenbeinküste, Accra/Ghana, Lagos/Nigeria, Douala/Kamerun und zurück bis Rotterdam.
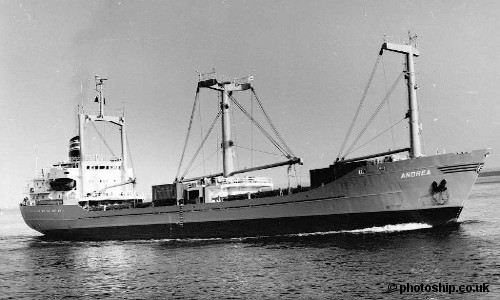
Bildquelle: photoship.co.uk
M/S "Andrea"
|
Reederei Hugo Bartels, Hamburg
Flagge: Deutschland
Bauwerft: Sietas Werft, Hamburg
Baunummer: 612
Frachtschiff
Baujahr: 1970
Tragfähigkeit: 4.543 tdw
1 MAK-Diesel mit 2,942 kW
Geschwindigkeit: 15,5 Knoten
Unterscheidungssignal: DHGL
IMO: 7015262
Die Reise war in Charter für die Deutsche Afrika Linie - vormals Woermann Linie - von Hamburg nach Abidjan/Elfenbeinküste, Accra/Ghana, Lagos/Nigeria, Douala/Kamerun und zurück bis Rotterdam.
|

Hamburg/Deutschland
|

Abidjan/Elfenbeinküste
|

Accra/Ghana
|

Lagos/Nigeria
|

Douala/Kamerun
|

Rotterdam/Niederlande
|
Unternehmensberaterfirma
Vielleicht als letzte Rettung holte man sich eine Unternehmensberatungsfirma ins Haus. Es wurden Gruppen gebildet, dann mussten von den Teilnehmern Testbögen ausgefüllt werden. Diese beinhalteten einige Querdenkerfragen und man musste die Fragen wirklich ganz genau lesen, da viele Haken und Ösen eingebaut waren. Auch ich - wie andere auch - bin auf einige hereingefallen.
Nach meiner Meinung sollte dieses Unterfangen eigentlich dazu führen, dass der Betrieb wirtschaftlicher wird. In einigen Bereichen war für die vorhandene Arbeit ein Überangebot an Personal. Aber in dieser Hinsicht tat sich nichts. Es wurde lediglich eine Arbeitsgruppe gebildet, ich glaube es waren 10 bis 12 Leute aus der Sparte Klarsichtfensterbau. Durch „Brainstorming“ sollten hier Einsparungspotentiale erarbeitet werden. Da das eigentliche Klarsichtfenster lediglich aus einem Rahmen, einer runden Glasscheibe und einem E-Motor mit Riemenantrieb bestand, konnte ich diesen Arbeitskreis nicht nachvollziehen. Die Gruppe kam in regelmäßigen Abständen wochenlang zusammen und das Ergebnis war gleich Null. Um überhaupt ein Ergebnis präsentieren zu können, hat man etwas an der Verpackung geändert. Mit anderen Worten: „Außer Spesen nichts gewesen!“ Auch das war Krupp-Atlas.
|
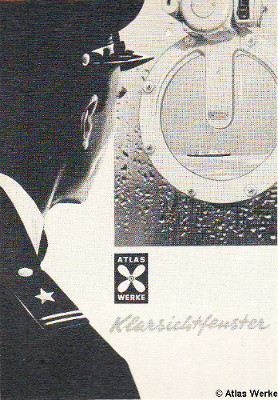
Atlas Werbung für Klarsichtfenster
|
Auch das gab es bei Krupp-Atlas.
Eine gemeinsame Freimarkt-Feier der Bauabteilung mit Freunden in der "Alten Gilde" - Altstadt von Bremen.
Frühjahr 1974 - Streik
Im Frühjahr 1974 legte ein Streik der IG Metall einen Großteil der metallverarbeitenden Betriebe in Norddeutschland lahm. Dazu gehörte auch unser angeschlagener Betrieb. Es wurden von der Gewerkschaft Streikposten organisiert, so dass keine Streikbrecher das Werk betreten konnten. Für einige der Belegschaft kam der Streik zur rechten Zeit. Es waren die, die sowieso keine große Lust hatten, im Betrieb zu arbeiten. Sie bestellten jetzt lieber ihre Gärten. Gerade jetzt, wo es Atlas zunehmend schlechter ging, organisierten wir auf der Weserseite –- uneinsehbar für die Streikposten an den Werkstoren - eine kleine Gruppe, die des Nachts einige zum Versand bereite Meerwasserentsalzungsanlagen auf bereitstehende Kähne verluden. Trotz des Streiks haben wir somit vertragsgemäß unsere Produkte an unsere Kunden ausliefern können.
Oktober 1974 – BAU Lehrgang
Von Mitte Oktober bis Mitte November 1974 absolvierte ich in Dortmund bei der BAU den Lehrgang zum Sicherheitsingenieur.
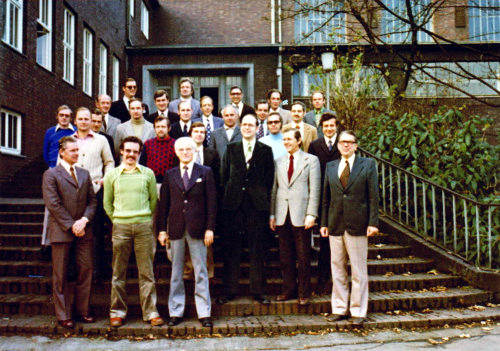
Teilnehmer am Lehrgang für Sicherheitsingenieure bei der Bundesanstalt für Unfallforschung "BAU" in Dortmund
|
1. Januar 1975 - Sicherheitsingenieur
In der Zeit vom Lehrgang in Dortmund bis zu meiner Einstellung als Sicherheitsingenieur hatte ich schon einige Ideen zur Umsetzung meiner Vorhaben ausgearbeitet. Ein wichtiges Ziel war es, alle Ressortchefs über ihre Pflichten und Konsequenzen zu informieren. Beim Führungspersonal herrschte noch immer die Meinung, dass sie nur für ihre Arbeiten verantwortlich waren. Sie wurden auf speziellen Betriebsversammlungen unterrichtet und geschult. Viele konnten einfach nicht glauben, wie groß ihr Verantwortungsbereich war. Es kostete schon einiges an Überzeugungsarbeit, dass diese Herren bezüglich des neuen Arbeitssicherheitsgesetzes mitarbeiteten.
Da in einigen Krupp-Betrieben schon seit längerem Sicherheitsingenieure arbeiteten, gab es im Werk Essen einen übergeordneten Sicherheitsingenieur, der in regelmäßigen Abständen Treffen mit Werksbegehungen in wechselnden Standorten zum Erfahrungsaustausch organisierte. Von den Erfahrungen der schon Jahre im Beruf tätigen SI's habe ich vieles auf unseren Betrieb übertragen können.
Ein Beispiel von vielen: Alle Krananlagen sowie Hebezeuge mussten in einem bestimmten Zeitraum einer Sicherheitsprüfung unterzogen werden – ähnlich wie ein PKW beim TÜV. In der Vergangenheit habe ich als Betriebsingenieur diesen Ablauf organisiert und ausgeführt. Ab jetzt wurden die zu prüfenden Anlagen mit weit sichtbaren Plaketten versehen, auf denen der nächste fällige Prüftermin vermerkt war. Die dafür verantwortlichen Ressortchefs waren nun für die rechtzeitige Überprüfung verantwortlich. Es war nicht so einfach, den alten "Schlendrian" aus den Köpfen der Leute zu bekommen. Durch ständiges Schulen und Mahnen ging es von Zeit zu Zeit besser.
Arbeitsunfälle wurden ab sofort analysiert und untersucht, warum, wieso, weshalb der Unfall passiert war. Die Unfallquellen mussten von den Verantwortlichen in einer bestimmten Zeit behoben und dem Arbeitsschutz gemeldet werden.
Die Erfolge, die ich mir eigentlich gewünscht hatte, ließen sich in der prekären Lage, in der sich Krupp-Atlas zu der damaligen Zeit befand, sehr schwierig durchsetzen. Ich hatte mir das etwas anders vorgestellt.
Mai 1975 - Dampfer „Welle“
Im April 1975 kaufte ein österreichischer Gastronom den Bremer Dampfer „Welle“, welcher 1914 bei den Atlas-Werken gebaut wurde und in Bremerhaven stationiert war. Das Schiff hatte man 1975 wegen zu hoher Betriebskosten und ständiger Rauchbelästigung außer Betrieb genommen. Der neue Eigner ließ das Schiff zu seinem Geburtsort „Atlas“ schleppen, um es hier in überwiegender Eigenarbeit in ein Gastronomieschiff umzubauen.
|
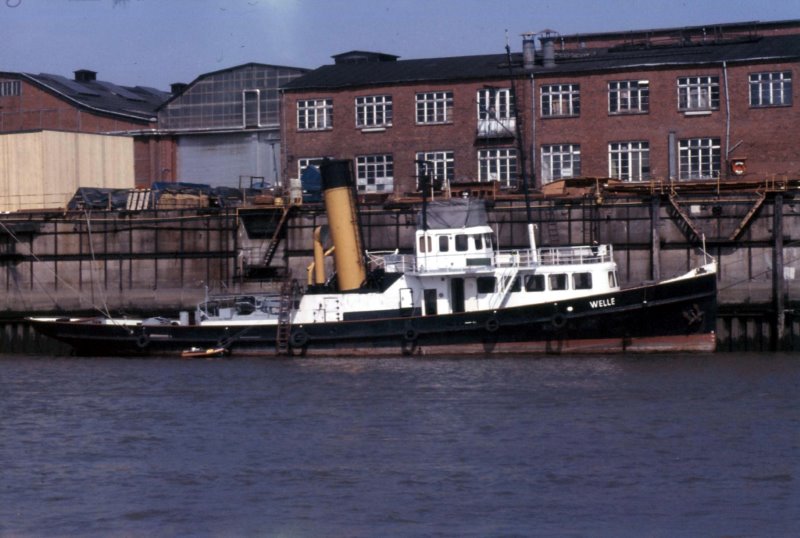
Mit freundlicher Genehmigung durch: Bodo Wenz, Bremen
Dampfer "Welle" hat bei Krupp-Atlas festgemacht
|
Dampfer "Welle" während des Umbaus bei Krupp-Atlas
|
Im Rahmen der Möglichkeiten hat Atlas den Umbau unterstützt. Eines Tages wurde vom Eigner einer seiner Mitarbeiter vermisst, keiner wusste wo er geblieben war. Einige Wochen später beim Verholen des Schiffes in ein Dock trieb die Leiche des vermissten Mannes auf. Er musste sich irgendwo zwischen Schiff und Kaimaier eingeklemmt haben. Ein schlechtes Omen für das Schiff?
|
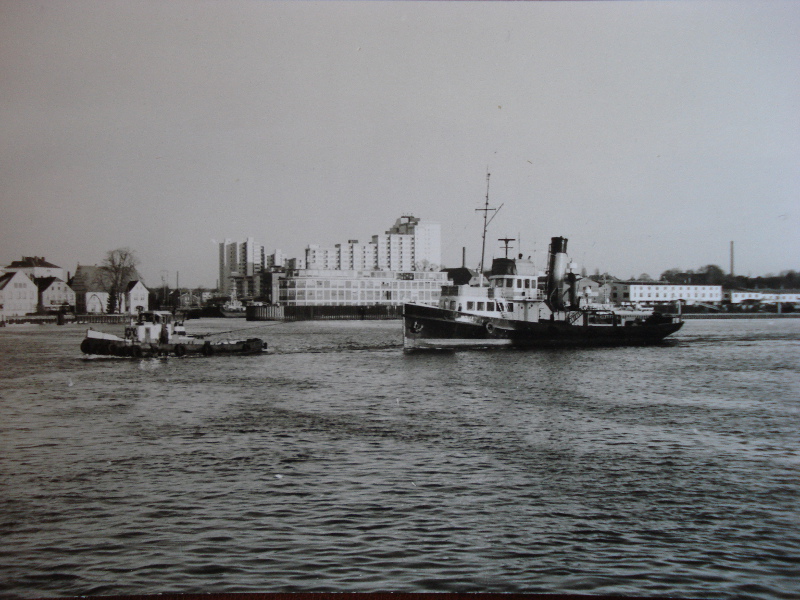
Mit freundlicher Genehmigung durch: Bodo Wenz, Bremen
Dampfer "Welle" im Schlepp weserabwärts ins Trockendock. Dort soll sie einen neuen Unterwasseranstrich bekommen bevor es an den endgültigen Liegeplatz geht.
|
Am Himmelfahrtstag 1976, kurz vor der offiziellen Eröffnung am neuen Liegeplatz an der Tiefer in Bremen, wurden ein paar Freunde und ich vom Besitzer zu einem Umtrunk auf dem neuen Schiff eingeladen. Der Ponton und die Gangway zum Schiff waren noch nicht fertiggestellt. Wir mussten zur Welle mit einem Schlauchboot übersetzten. Ich war beeindruckt von der maritimen Atmosphäre auf dem Schiff. Vieles war im Originalzustand erhalten und viele maritime Gegenstände, wie alte Schiffslampen der Firma Ahlemann & Schlatter waren installiert worden.
|
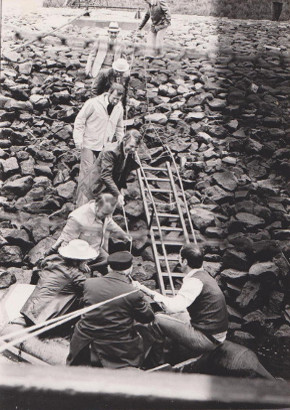
Schwieriger Abstieg, der Eigner Herr Heis nimmt uns in Empfang
|
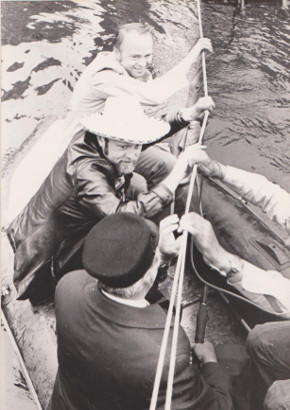
Übersetzen mit einem Schlauchboot zur "Welle"
|
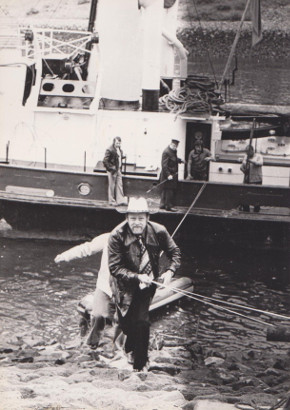
leicht angeheitert geht es zurück
|
|
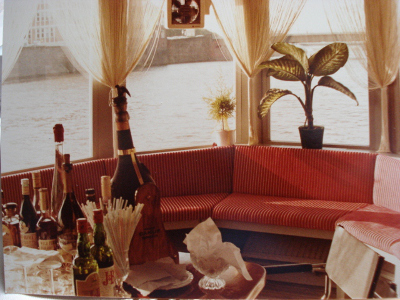
Mit freundlicher Genehmigung durch: Bodo Wenz, Bremen
|
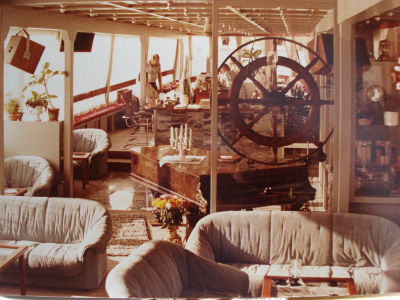
Mit freundlicher Genehmigung durch: Bodo Wenz, Bremen
|
Das Schiff hatte man bis zu diesem Zeitpunkt in seiner äußerlichen Silhouette belassen.
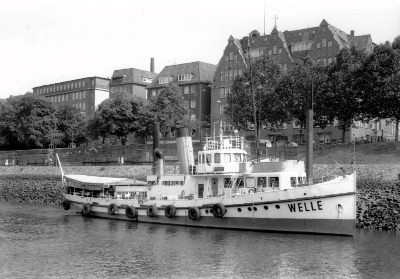
Mit freundlicher Genehmigung durch: Bodo Wenz, Bremen
Dampfer "Welle" bei Tag
|
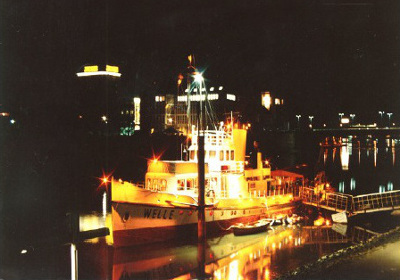
Mit freundlicher Genehmigung durch:
www.Verein Dampfer Welle eV
. . . und bei Nacht
|
|
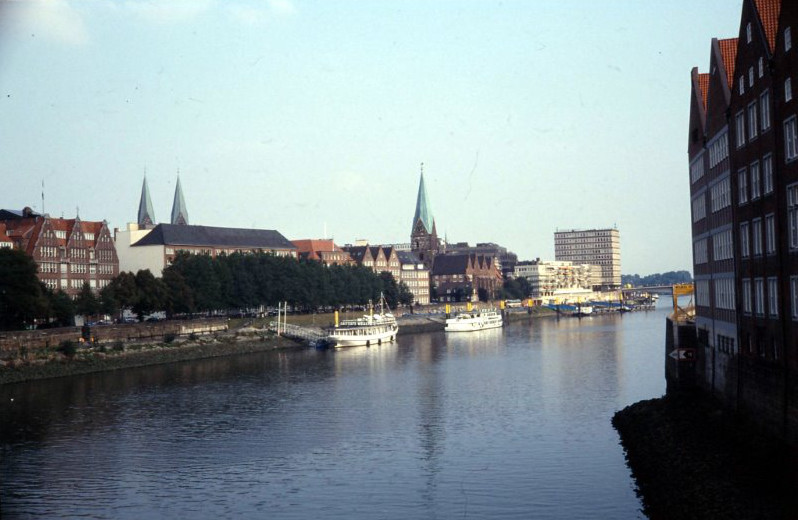
Mit freundlicher Genehmigung durch: Bodo Wenz, Bremen
Dampfer "Welle", der jetzt schon viel von seiner Ursprünglichkeit verloren hat, an seinem Liegeplatz an der Tiefer in Bremen
|
Nachtrag zum Verbleib des Schiffes:
Das Schiff wurde später bis zur Unkenntlichkeit verschändelt. Es brannte mehrfach aus und sank. Ein gemeinnütziger Verein „Dampfer Welle Bremen“ nahm sich seiner an und restauriert das Schiff, damit es zum 100. Geburtstag wieder im Originalzustand fahren kann. Ein Klick auf die "Welle" und schon ist man an Bord des historischen Dampfers.
September 1975 – SBG Lehrgang
Im September 1975 absolvierte ich zusätzlich einen 14-tägigen Lehrgang
“Fachkräfte für Arbeitssicherheit“ der Seeberufsgenossenschaft an der Hochschule für Nautik und Technik.
Am Kursus nahmen ausschließlich Kapitäne und leitende Ingenieure teil. Da ich aus der Industrie kam und schon einige praktische Erfahrungen sammeln konnte, fragte man mich von Seiten der Hochschule, ob ich Interesse habe, bei den nächsten Lehrgängen als Dozent aus der Praxis zu unterrichten? Die Tätigkeit als Gastdozent brachte mir viel Spaß. Auch die Teilnehmer waren über meine Vorträge begeistert.“
Januar 1976 - Sturmflut
Am 3. und 4.1.1976 wütete wieder ein schwerer Orkan über Bremen. Diesmal war der Sturm nicht so heftig, dafür aber die schwerste Sturmflut seit Februar 1962. Der Pegelstand der Weser lag bei 4,76 m üNN. Trotz erhöhter Deiche kam es an einigen Stellen zu Überschwemmungen.
Das Hochwasser machte auch vor Atlas nicht Halt. In dem Trakt des ehemaligen Werftgebäudes, wo ich im Untergeschoss mein Büro hatte, stieg das Wasser ca. 20 cm über den Fenstersims. Ich hatte rechtzeitig meine wichtigsten Akten in die Obergeschosse gebracht, denn keiner wusste wie hoch das Wasser steigt und ob die Fensterscheiben dem Wasserdruck bzw. den vorbeischwimmenden Gegenständen stand hält. Es ist hier alles ziemlich glimpflich verlaufen. Die Hochwasserschieber zu den sehr tief liegenden Waschkauen wurden geschlossen und die im Werkshafen schwimmenden Schuten gesichert. Was wir nicht verhindern konnten, waren Sturmschäden an Gebäuden, Dächern und Gerüsten.
Vieles wurde gesichert, egal ob Ausgänge zugemauert oder die Schuten im Werfthafen auf Abstand gehalten werden mussten. |
Am Abend stand das Wasser bis zum Fenster meines Büros und des Nschts über dem Fenstersims |
Der höchste Wasserstand war erreicht. |
|
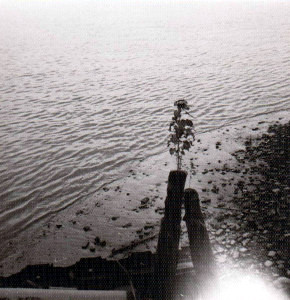
. . . und so es es wieder bei normalen Wasserstand aus.
|
Warum dieser Zaun?
Was sich jetzt in den letzten Monaten bei Krupp-Atlas tat, konnte ich beim besten Willen nicht nachvollziehen. Innerbetrieblich gab es bezüglich „Erneuerungen“ nicht viel. Stattdessen wurde die Umzäunung des Werksgeländes zur Stephaniekirchenweide mit dem teuersten „Bongossi-Edelholz“ erneuert. Warum dieses Vorhaben? Ich verstand es nicht. Aber hierfür war ich nicht mehr zuständig, es war die Angelegenheit meines Nachfolgers.
Ich frage mich heute noch immer, wo wohl dieser Zaun jetzt steht!
Ersatzteile und Lager
Die Instandhaltung und Reparatur des Werkzeugmaschinenparks fiel, wie Eingangs schon erwähnt, in meinen Verantwortungsbereich. Viele dieser Maschinen hatten schon etliche Jahre auf dem Buckel. Wir waren froh, bei Bedarf von den jeweiligen Herstellern möglichst umgehend mit Ersatzteilen versorgt zu werden. Für Atlas war das selbstverständlich.
Aber es gab auf der Welt auch viele Atlas-Erzeugnisse, die mit Ersatzteilen versorgt werden mussten mit dem "kleinen" Unterscheid, dass unsere Lieferzeit 3 bis 6 Monate betrug. Ein Ersatzteillager gab es nicht, aber man hätte den Kundenservice verbessern müssen. Laut Arbeitsvorbereitung war das angeblich nicht möglich. Insbesondere für Schiffshilfsmaschinen bedeutete das einen großen Imageverlust. Ich wusste es aus eigener Erfahrung zu gut, was es heißt, wenn man zum Beispiel für eine Bilgenwasserlenzpumpe an Bord eines Seeschiffes 6 Monate auf ein Ersatzteil warten musste.
Da ich einen guten Draht zum Außendienst hatte, haben wir bei den nächsten Ersatzteilaufträgen die Arbeitsvorbereitung umgangen und den organisatorischen Ablauf vereinfacht. Eine schnellere Auslieferung war also möglich.
In der Zeichenausgabe waren alle Zeichnungen verfügbar, also holten wir uns die entsprechende. Selbstverständlich war auf den Zeichnungen die Materialqualität angegeben. Jetzt wurde von uns eine Materialbegleitkarte ausgestellt – und direkt dem Verwalter des Stangenmateriallagers mit dem Vermerk „EILT“ übergeben. Das lag in unserer Befugnis.
Das Stangenmateriallager befand sich im Freien. Hier herrschte ein unglaubliches Chaos. Die Farbmarkierungen waren verwittert und/oder die Beschilderungen der Materialqualitäten, Chargennummer, Hersteller, Testnummer etc. fehlten. Oft war eine eindeutige Materialidentifizierung nicht mehr möglich. Gestempeltes Material wurde mit der Stempelung abgesägt und nicht wieder ergänzt. Wo blieb da die Schulung des Personals?
Der lange Weg über die angeblich unverzichtbare Arbeitsvorbereitung war umgangen und die Teile konnten nach einigen Tagen ausgeliefert werden.
Das Blechlager am Ende des Werksgeländes, welches früher hauptsächlich für den Schiffbau benutzt wurde, war genau so chaotisch. Die Bleche lagen im Freien übereinander auf dem Boden. Benötigte man ein bestimmtes Blech, musste dieses durch Umstapeln gesucht werden bis man fündig wurde - wenn überhaupt. Zur Zeit des Schiff- und des einfachen Behälterbaus ging das vielleicht mit seinen 2 oder 3 Blechqualitäten noch soeben. Aber was für ein zeitaufwändiger Zustand. Tatsächlich hatte man ein neues Lager gebaut, in dem die Bleche senkrecht in Boxen plaziert wurden. Sie konnten jetzt besser markiert und einfacher mit Transportklammern bewegt werden. Jetzt kommt wieder ein "Aber", denn den Kran für das Blechlager kaufte man aufgrund von Kompensationsgeschäften in der damaligen DDR. Der Kran stand mehr als dass er lief und so dauerte der Blechtransport genau so lange wie beim alten Blechlager - auch das war Atlas.
Ein Ersatzteillager gab es allerdings doch bei Krupp-Atlas. Es handelte sich um Berge fremdgefertigtem Rohmaterial, wie zum Beispiel Kettenräder für Ankerwinden etc. Diese standen mit hohen Beträgen als Guthaben in den Büchern. Beim Verkauf der Schiffshilfsmaschinensparte hatte man vergessen, diese Teile mit zu veräußern. Jetzt hatten sie nur noch Schrottwert und mussten abgeschrieben werden.
Die Verschleißplatten für die Krupp-Atlas Kalksandstein – sowie Betonsteinpressen waren eigentlich ein lohnendes Geschäft für uns. Aber die Sache hatte einen Haken, eine Konkurrenzfirma, die sich auf diese Platten spezialisiert hatte, war smarter. Die Qualität war um ein Vielfaches besser und entriss Krupp-Atlas dieses lohnende Geschäft. Um dieses Geschäftsfeld wieder zurückzugewinnen, wurde für über 1 Million DM eine komplett neue Fertigungsstraße einschließlich Härterei gebaut. Die Sache hatte nur einen Haken, die Atlas-Platten bekamen immer wieder an den kritischen Punkten Härterisse. Die Konkurrenz hatte dieses Problem mit einer kleinen technischen Veränderung ausgemerzt und sich patentieren lassen. Eigentlich hätte das jeder Konstrukteur wissen müssen, auch bei Atlas. Fazit der Geschichte: die neue Fertigungsstraße wurde zum Flop und 'ne Million war mal wieder futsch. Auch das war Krupp-Atlas.
Flexibilität spielte keine Rolle, sondern Firmentreue war wichtig.
Die Belegschaft wurde nicht auf die sich veränderten Bedürfnisse umgeschult.
Hier ein paar Beispiele von vielen:
Die Arbeitsvorbereitung war langsam und träge, hier gab es keinen, der mal mit der Faust auf den Tisch haute.
Die veralteten Laufkräne in den Hallen waren noch immer mit Kranfahrern besetzt. Benötigte man einen Kran, waren die Fahrer nicht da oder schliefen. Beim Umrüsten der ersten Krane von Korbbedienung auf Flurbedienung sträubten sich die Fahrer mit den Argumenten: „Was, jetzt soll ich neben dem Kran herlaufen, mal den einen oder den anderen Kran bedienen und Anschlagen der zu transportierenden Teile soll ich auch noch, das ist aber des Guten zu viel!“
Einige der Gerüstbauer aus meiner Bauabteilung waren Trinker. Ich konnte und wollte es nicht verantworten, dass ausgerechnet diese Leute angetrunken auf Gerüsten und/oder Hallendächern herumtollten. Abmahnungen waren nicht möglich, weil diese Mitarbeiter gute Freunde des Betriebsrates waren. Wenn ich sie suchte, waren sie beim Betriebsrat und tranken dort Kaffee. Das Trinken war ein Relikt aus der Zeit nach dem Krieg. Ich konnte mich noch gut an die Zeit bei Atlas erinnern, als ich noch Lehrling war. Zu jener Zeit konnte sich jeder Bier und andere Alkoholikas in der Kantine kaufen. Je mehr getrunken wurde, umso höher fiel zu Weihnachten die Rückvergütung des Kantinenüberschusses an die Belegschaft aus.
Ach ja Betriebsrat.
Ich fragte mich immer wieder, wie der von der Belegschaft gewählte Betriebsrat solche Missstände verantworten konnte. Der BR bestand aus Leuten, die keine Lust mehr zum arbeiten hatten, aus den unteren Lohnklassen kamen, die größte Klappe hatten und das richtige Parteibuch besaßen. Ein Beispiel: als ich Sicherheitsingenieur wurde, ist diese Arbeit nebenher vom Betriebsrat ausgeführt worden. Es wurde lediglich eine Strichliste geführt, auf denen vermerkt wurde, wo sich die Unfälle ereigneten. Analysen und Behebung der Unfallquellen, Fehlanzeige.
So war es fast überall im Betrieb. Es fehlte an Führungskräften, die auch mal sagten, du bist hier fehl am Platz, du kannst morgen deine sieben Sachen packen, das war es dann für dich!
Verdampfertechnikum
Auf dem alten Schräghelgen, wo man früher mal Schiffe und später Ruderblätter für die Riesentanker der AG Weser gebaut hatte, wurde ein großes Becken für Seewasser errichtet. Das Seewasser wurde mit Bargen angeliefert. Es stammte von im Hafen liegenden Schiffen, die beim Laden ihre Ballasttanks leeren mussten. Das Wasser wurde für ein provisorisch errichtetes Prüffeld, das sogenannte Verdampfertechnikum zu Erprobung von großen Meerwasserentsalzungsanlagen benötigt. Die neuen Umkehrosmose-Anlagen sollten unter realen Bedingungen getestet werden. Das Interesse an diesen Anlagen war in den arabischen Ländern besonders groß.
|
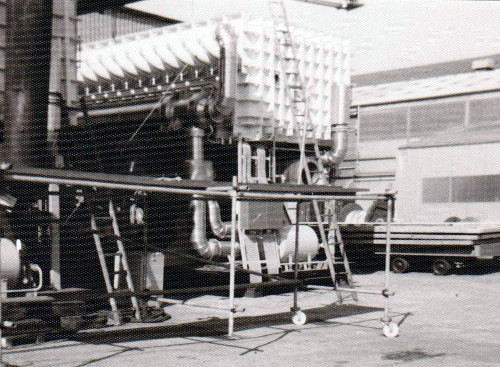
Meerwasserentzalzungsanlage auf dem Weg zum Prüffeld im Verdampfertechnikum
|
Kritik von Kraftwerkskunden
Die Besteller von Kernkraftwerkskomponenten, wie zum Beispiel Vorwärmern, bestanden zunehmend darauf, dass die Fertigungshallen staubfrei hergerichtet werden sollten. Die Hallen sahen eher nach Abbruch aus. Bei Krupp-Atlas bemühte man sich, diesem Anliegen nachzukommen. Die Hallenböden wurden Kunststoff beschichtet, was natürlich einen guten Eindruck machte. Aber die großen hohen Hallen mit ihren nach draußen fahrenden Laufkränen waren technisch bedingt sehr undicht. Es gab einfach für diese veraltete Konstruktion keine Lösung, die Kranschürzen besser abzudichten.
Diese Undichtigkeiten in den Hallen nutzten die Tauben als ihre "Heimat" zum Schlafen und Brüten. Sicherlich gab es auch genug Futter von den Arbeitern. Nun kam der Dreck als Scheiße von oben. Jetzt blieb als Sofortmaßnahme nichts anderes übrig, als die Produkte nach Feierabend mit Planen abzudecken. Wieder mal ein zusätzlicher Zeitaufwand. Weiter stellte sich die Frage, wie bekommen wir die Tauben aus den Hallen? Vertreiben war nicht möglich, vergiften kam aus Tierschutzgründen nicht in Frage. Mein ehemaliger Vorgesetzter holte sich die behördliche Genehmigung zum Abschießen der Tauben ein. Aber wer sollte es machen? Da ich mir kurz zuvor offiziell ein Kleinkalibergewehr mit Zielfernrohr gekauft hatte, erklärte ich mich für diese außergewöhnliche Aktion bereit. Allerdings durften die Tauben nur unter ganz besonderen Bedingungen und zu festgelegten Zeiten geschossen werden.
Beim ersten Mal war der Erfolg vielversprechend. Allerdings musste die Bauabteilung zu Wochenbeginn die von mir in den Hallendächern verursachten Schusslöcher abdichten. Am zweiten Wochenende war der Erfolg recht dürftig, denn die Tauben verschwanden nach dem ersten Schuss und kamen erst wieder zurück, als Ruhe eingekehrt war. Am dritten Wochenende verschwanden sie sofort, als wir anrückten. Die Tiere sind ja auch nicht so dumm. Als weitere Maßnahme wurde ein präparierter Mais auf den Dächern als Futter verstreut. Es handelte sich um ein Präparat - beim Menschen die Antibabypille - welches bei den Tauben die Eier unfruchtbar machen sollte. Auch das war Krupp-Atlas.
Neuer IBM-Rechner
Im ehemaligen Elma-Trakt, wo lediglich das Labor untergebracht war, wurde eine neue IBM-Anlage für die Lochkartenverarbeitung der Lohnbuchhaltung installiert. Dort hatten die Herren Programmierer in edlen Anzügen mit überdurchschnittlichen Gehältern das Sagen. Wenn diese Herren sagten, hier stinkt es, dann bekamen sie eine neue Klimaanlage mit Frischluftzufuhr, denn keiner der anderen leitenden Angestellten wusste genau, was da abläuft. Auch das war Krupp-Atlas!
1976 - die letzten Investitionen
Im KKW-Biblis A wurde schon seit Wochen am Speisewasserbehälter sowie Vorwärmern repariert. Zur gleichen Zeit wurden bei Atlas einige Investitionen eingeleitet. Die alte Lehrwerkstatt - das weit sichtbare Wahrzeichen - mit der Zimmerei wurde abgerissen. Die davor gelagerte Halle, die senkrecht zur Kaimauer stand, wurde komplett umgebaut. Sie erhielt zwei neue Laufkräne mit jeweils 20 Tonnen Tragkraft sowie einen Schienenstrang, der direkt zur Kaimauer führte. Hier sollten bis zu mehreren 100-Tonnen schwere Mehrlagenbehälter gefertigt werden. Das Werk Rheinhausen wollte die Fertigung nach Bremen verlagern - aus welchem Grund auch immer. Die Behälter sollten dann auf der eigens dafür geschaffenen Gleisanlage bis an den werkseigenen Kai gefahren werden und anschließend von den beiden Kranschiffen "Energie" und "Ausdauer" der Schuchmann-Reederei über die Weser in alle Himmelsrichtungen abtransportiert werden.
Ich habe mich damals schon gefragt, ob das Vorhaben wohl gut geht? Die Kaimauer war derartig marode und die Tide fraß immer größere Löcher hinein. Sie sah aus wie ein schweizer Käse. Ich hatte auf die Misere hingewiesen, aber ich stieß damit bei den zuständigen Herren mal wieder auf taube Ohren. Für mich war diese Investition ein totgeborenes Kind – und ich sollte mal wieder recht behalten. Wäre es tatsächlich zum Bau derart schwerer Behälter gekommen, wäre die Kaimauer beim Verladevorgang unweigerlich zusammengebrochen und der Behälter hätte im Hafen gelegen. Ich selbst sah durch dieses Vorhaben keine Zukunft mehr bei Atlas und schmiedete schon im Hinterkopf neue Pläne.
Was sich jetzt in den letzten Monaten bei Krupp-Atlas tat, konnte ich beim besten Willen nicht nachvollziehen. Innerbetrieblich tat sich bezüglich „Erneuerung“ nicht viel, aber die Umzäunung des Werksgeländes zur Stephaniekirchenweide wurde mit dem teuersten „Bongossi-Edelholz“ erneuert. Warum dieses Vorhaben? Meine Oma sagte oft: Oben wie ein Pfau und unten wie 'ne Sau. Das traf auch hier zu, nämlich: Außen wie ein Pfau und innen wie 'ne Sau. Aber hierfür war ich nicht mehr zuständig. Es war die Angelegenheit meines Nachfolgers.
Oft habe ich mich gefragt, wo wohl dieser Zaun jetzt steht?
Juni 1976
Trotz aller Bemühungen geriet Krupp-Atlas nach meiner Meinung zunehmend in Schieflage. Die Auftragssituation sah nicht gut aus. Reklamationen der Kraftwerksbetreiber wegen Risse in den Speisewasserbehältern vermehrten sich. Vielleicht standen auch noch Regressansprüche an.
1976 – Reparatur des Speisewasserbehälters im KKW Biblis A
Info: KKW-Biblis A
Am 16. Juli 1974 wurde in Block A die erste Kettenreaktion eingeleitet und lieferte am 25. August 1974 erstmals Strom ins öffentliche Netz.
Im Mai 1976 wurde ich zu einem Gespräch der Geschäftsleitung gebeten, ob ich bereit wäre, für eine befristete Zeit die Reparaturarbeiten des Speisewasserbehälters in KKW Biblis A zu koordinieren und zu beaufsichtigen. Da ich zur damaligen Zeit noch ein großer Befürworter der Kernenergie war, sagte ich sofort zu. Es war eigentlich schon immer mein Traum, einmal in einem KKW zu arbeiten. Zu meiner Seefahrtzeit hatte ich mich um eine Urlaubsvertretung auf dem einzigen deutschen atomgetriebenen Frachter N/S „Otto Hahn“ beworben, erhielt aber eine Absage. Diese Arbeit könnte für meine Zukunft nach Atlas möglicherweise von Vorteil sein. Allerdings sehe ich heute die Nutzung der Atomenergie auf Grund des Fukushima-Desasters mit etwas anderen Augen. Eigentlich hätte dieser Job von einem qualifizierten Schweißfachingenieur ausgführt werden müssen. Aber wie schon zuvor bei der Seefahrt sagte ich mir: "Geht nicht - gib`s nicht!" und so machte ich diesen Job bis zur erfolgreichen Druckprobe.
Nach einer kurzen Besprechung mit den Verantwortlichen, die für die Reparaturarbeiten zuständig waren – ich als hauptamtlicher Sicherheitsingenieur hatte ja keinen Vorgesetzten mehr, da ich nach dem Arbeitssicherheitsgesetz direkt der Geschäftsleitung unterstellt war – setzte ich mich in meinen BMW und fuhr nach Worms. Allerdings wurden diese Fahrten zum Albtraum. Die RAF, die es noch immer gab, fuhren auch BMW, so dass ich von einer in die nächste Polizeikontrolle geriet. In einem kleinen Hotel bezog ich mein Quartier und dann begab ich mich direkt zum KKW Biblis Block A. Nach den üblichen Formalitäten beim Sicherheitscheck betrat ich erstmals ein KKW.
|
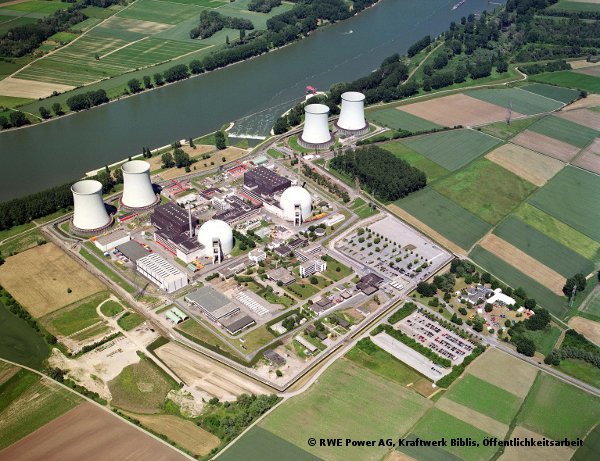
Mit freundlicher Genehmigung: RWE Power AG, Kraftwerk Biblis, Öffentlichkeitsarbeit, dd. 10. 1. 2011
Luftaufnahme KKW Biblis Block A und B
|
Ich wurde direkt zu meiner neuen Baustelle eskortiert. Hier verschaffte ich mir erst mal einen Überblick über die Örtlichkeiten und die anstehenden Arbeiten. Als ich den Behälter sah, war ich von seiner Größe überrascht.
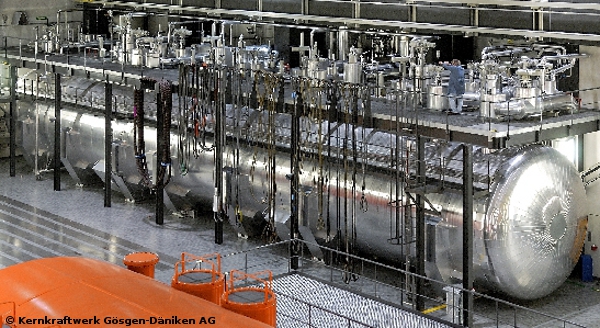
Mit freundlicher Genehmigung: Kernkraftwerk Gösgen-Däniken AG, Abteilung Kommunikation dd. 19. 8. 2013
www.kkg.ch-info
Der Speisewasserbehälter des Schweizer KKW Gösgen gleicht dem von Biblis
|
Er hatte die folgenden Abmessungen:
Länge: 50m
Durchmesser: 4m
Auslegungstemperatur: 200°C
Inhalt: 620m3
Betrieblich ca. 320 m3 Wasserinhalt
|
Man konnte nur durch die unteren Mannlöcher ins Innere des Behälters gelangen. Kabel und Schläuche jeglicher Art, die auch die Mannlöcher verlegt waren, erschwerten den Einstieg. Zur Be- und Entlüftung waren oben auf dem Behälter einige Ventile demontiert worden. Im Behälter arbeiteten im Schnitt 30 bis 40 Personen. Mir als Sicherheitsing. standen buchstäblich die Haare zu Berge, als ich dieses Gewurschtel und Gewirr von Leuten und Gerätschaften sah. Eigentlich hätte die Baustelle stillgelegt werden müssen, aber ich war ja speziell für diesen Job als Sicherheitsingenieur entbunden worden und hatte zugesagt, diese Arbeit auszuführen. Im Inneren des Behälters befanden sich eine Vielzahl von Rohren und Prallblechen. Die Halterungen hierfür waren mit der Behälterwand verschweißt und hier traten vermehrt Risse auf, denn der Behälter war mit einem neuartigen Feinkornbaustahl anstatt des damals bewährten H II Kesselblech gefertigt worden. Alle Halterungen, Stutzen etc. wurden mittels Ultraschall auf Risse überprüft und die defekten Teile abgetrennt.
Ja, jetzt kam eine Zeit, die mich fast in den Wahnsinn trieb. Hier sagte ich stets zu mir: „Ralf, bleib ruhig“!
Alle Fehlstellen im und am Behälter wurden markiert und nummeriert. Die „Verantwortlichen“ erstellten eine riesige Checkliste, wo später alle einzelnen Reparaturschritte abgezeichnet werden mussten. Es kamen immer neue Fundstellen hinzu, was die Aktualisierung der Checkliste und die laufenden Arbeiten erschwerte. Aber wer war nun wofür verantwortlich? Es gab ein für mich nie nachvollziehbares Kompetenzgerangel zwischen:
RWE, dem Betreiber des KKW Biblis A
TÜV-Rheinland, weil der Hauptsitz der RWE in Essen ist
TÜV-Norddeutschland, weil für Behälterbauer Krupp-Atlas in Bremen zuständig
Technischer Überwachungsverein Hessen, weil der Standort Biblis in Hessen ist
KWU als Erbauer des Kraftwerkes
Atombehörde für Kernkraftwerke in Deutschland mit Sitz in Bayern
MPA-Stuttgart, Reaktorsicherheitskommission unter Leitung von Professor Karl Kußmaul
Jeder wollte das Sagen haben und mich guckte man als Prügelknaben aus, weil ich in deren Augen die Misere zu verantworten hatte.
Während dieser Phase erlaubte es die Zeit, daß ich mir das Kraftwerk in allen Einzelheiten zeigen und erklären lassen konnte. Ich war von der Größe einiger Anlagenteile schon überrascht. Dazu gehörten die Pumpen und Rohre der Kühlwasserversorgung aus dem Rhein. Die Turbine und den Generator hatte ich mir größer vorgestellt.
Hier nun noch einige Daten vom KKW Biblis A:
Druckwasserreaktor
1300 MW
Kühlturmhöhe 80 m hoch, Durchmesser 68 m
Kühlwasserleitungen ca. 2,50 m Durchmessert
|
|
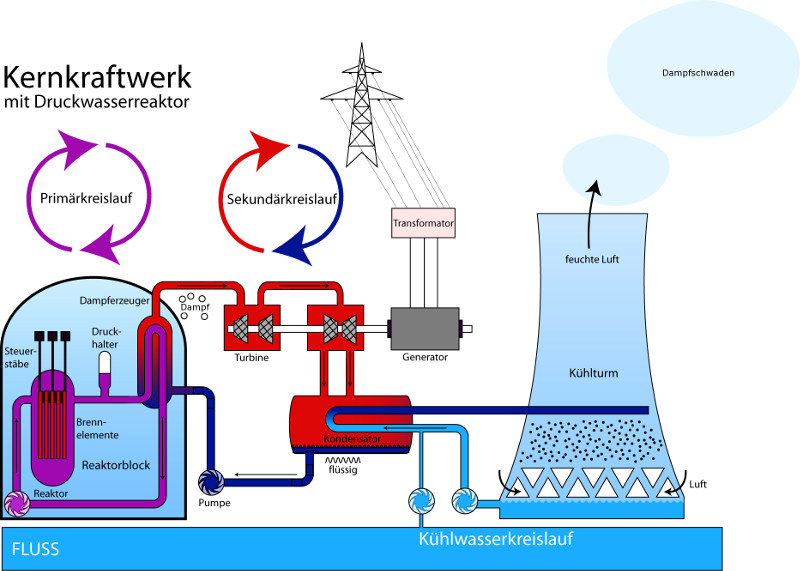
Bildquelle: wikimedia.org
Die wirkungsweise eines Druckwasserreaktors
|
Nachdem sich die Herren auf den Ablauf der Reparaturarbeiten geeinigt hatten – das glaubte ich – begannen die eigentlichen Probleme.
Jeder einzelne Arbeitsschritt ob Schleifen, Rissprüfung, Schweißen, die Vorwärmzeit der Schweißelektroden, der Elektrodentyp, die Vorwärmtemperatur des Behältermantels etc. musste vorher in der Checkliste von den dafür vorgesehenen Personen abgezeichnet werden. Es wurde schon mal von den Arbeitern vergessen, diesen Ablauf einzuhalten, oder die dafür verantwortliche Person war nicht aufzufinden. Wehe dem, wenn der zweite Schritt vor dem ersten erfolgte. Keiner nahm die Schuld auf sich, keiner hatte Schuld. Es war ein Chaos ohne Ende, wodurch sich die Arbeiten verzögerten. RWE übte ordentlichen Druck auf eine schnellere Erledigung der Arbeiten aus, denn jeder Tag Stillstand kostete dem Betreiber 1 Million DM. Ein großer Schwachpunkt war die zu geringe Anzahl von geprüften NDE-Leuten (zerstörungsfreies Prüfen von Oberflächenrissen und Ultraschall). Da ich hier so gut wie auf verlorenem Posten stand, organisierte ich die fehlenden Fachkräfte von einer namhaften Firma für zerstörungsfreie Prüfungen. Ich dachte mir, irgend jemand wird die Kosten schon übernehmen.
Exakt in der heißen Phase der Reparaturarbeiten wurden einige Eurpapokalspiele der Landesmeister mit Borussia Mönchengladbach live im Fernsehen übertragen. Es war eine sehr schwierige Zeit, die Leute bei der Stange zu halten.
In regelmäßigen Abständen fuhr ich für ein paar Tage zurück nach Krupp-Atlas. Bei einer meiner Reisekostenabrechnungen passierte mir mal ein Fehler. Anstatt 0,4 Pfennig abzurunden, habe ich diesen auf 1 Pfennig aufgerundet. Es ist nicht zu glauben, dass ich mich wochenlang mit der Buchhaltung wegen dieses einen Pfennigs gestritten habe. Es gingen laufend Pamphlete hin und her, bis ich eines Tages die Schnauze voll hatte und den Pfennig korrekt per Banküberweisung zurückzahlte. Ich riss mir für die Firma "den Arsch auf" und holte für sie die Kastanien aus dem Feuer. Der Dank dafür waren diese Nickeligkeiten.
In regelmäßigen Abständen ging ich frühmorgens zum Filter, in den das Flusswasser zu den Kühlwasserpumpen eingeleitet wurde. Ab und zu zappelte dort ein großer Fisch, den wir rausholten und am Abend grillten.
An einem Wochenende wurde bei einer Nacht- und Nebelaktion ein großer Stutzen oben am Behälter rausgebrannt und zur MPA nach Stuttgart gebracht. Dort sollte das Behälterblech sowie die Schweißung auf Laminate etc. untersucht werden. Über die Ergebnisse habe ich keine Kenntnisse.
Nach ca. 6-monatiger Reparatur stand endlich die Druckprobe an. Aber die erwies sich problematischer als ich gedacht hatte. Es wurde Wochen vorher bis hin zur hessischen Landesregierung darüber diskutiert und beraten. Normalerweise ist eine Druckprobe kein außergewöhnliches Ereignis. In diesem speziellen Fall muss dazu folgendes angemerkt werden:
Der Speisewasserbehälter steht auf fast gleicher Höhe wie die Dampfturbine mit Generator. Sollte wider Erwarten der Behälter mit seinen 630 m³ Inhalt bersten, würde das plötzlich austretende Wasser wie ein Tsunami Turbine und Generator mit sich reißen. Die Zerstörungen auf dieser sowie den darunter liegenden Etagen wären katastrophal. Aus diesem Grunde wurde der komplette Behälter mit Dehnungsmessstreifen versehen. Die kleinsten Unregelmäßigkeiten wurden dann sofort angezeigt. Notfalls konnte man die Prüfung sofort abbrechen. Der Kontrollstand wurde in einer sicheren Entfernung zum Behälter aufgebaut. Die Kommunikation zwischen dem Personal vom Kontrollstand und Behälter wurde mittels Kameras und Walkie-talkie sichergestellt.
Für die Druckprobe wurde aufbereitetes und angewärmtes Wasser verwendet, da das Behältermaterial sehr empfindlich auf kalte Temperaturen reagierte. Der Einzige, der sich hinter der Absperrung auf dem Behälter aufhalten durfte, war ich. Eventuell auftretende Leckagen an den Dichtungen, wie zum Beispiel Behälter/Ventil, wurden von mir soweit möglich behoben. Es war wohl eine der aufwendigsten Druckproben, die jemals in Deutschland ausgeführt wurden.
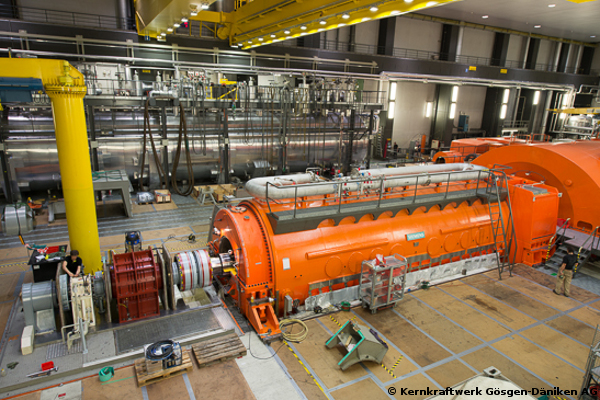
Mit freundlicher Genehmigung: Kernkraftwerk Gösgen-Däniken AG, Abteilung Kommunikation dd. 19. 8. 2013
www.kkg.ch-info
Der Speisewasserbehälter des Schweizer KKW Gösgen liegt wie in Biblis parallel zur Turbine und Generator
|
Die Druckprobe verlief ohne weitere Beanstandungen und bei den gutgekleideten Herren ging ein Aufatmen durch die Reihen. Es gab jedoch Einschränkung:
Der Betrieb durfte nur mit eingeschränktem Betriebsdruck weitergeführt werden, das bedeutete für Block A, er konnte nur mit Teillast betrieben werden.
Die Laufzeit wurde beschränkt.
Der Speisewasserbehälter musste in möglichst kurzer Zeit durch einen neuen ersetzt werden.
Nach Beendigung meiner Tätigkeit in Biblis trat genau das ein, was ich schon lange ahnte, es wurde eine größere Entlassungswelle angekündigt. Es deutete sich das Ende einer einstigen Weltfirma an. Wie soll ein Betrieb weiter existieren, der schon in guten Zeiten extrem hohe Gemeinkosten hatte? Ich bat die Geschäftsleitung um Auflösung meines Arbeitsvertrages mit einer entsprechenden Abfindung. Man kam meinem Wunsch nach. Der Personalchef hatte noch versucht, mich als Service- und Inbetriebnahmeingenieur für die Sparte Meerwasserentsalzungsanlagen zu gewinnen. Da die Kunden überwiegend aus den Öl- und Wüstenstaaten wie zum Beispiel Persien, Irak, Saudi Arabien, Kuweit, Libyen etc. kamen, sagte ich dankend ab. Da ich die Freiheit, Wein und Weib liebte, wäre ein Leben in einem Ghetto, bestehend aus Containern in der Wüste, kein Leben für mich. Hiermit war für mich auch der Job bei Krupp-Atlas erledigt. Im Dezember 1976 packte ich meine Sachen zusammen und verließ ohne Wehmut die Firma.
Epilog
Kurz nach meinem letzten Arbeitstag kam das endgültige "Aus" für Krupp-Atlas.
Ich war mehr als froh, die Abwicklung des Werkes nicht tätigen zu müssen. Es liegt nämlich in meinem Naturell, etwas zu schaffen und zu pflegen anstatt etwas abzureißen. Diese Arbeit sollten andere machen.
Mit dem Abfindungsgeld habe ich mich selbstständig gemacht. Leider lief mein Unternehmen nicht meinen Vorstellungen entsprechend. Durch die nicht immer unternehmerfreundliche Politik in Bremen wanderten viele Firmen ins niedersächsische Umland oder auch nach Hamburg ab bzw. alt eingesessene Bremer Familienunternehmen wurden an große Konzerne verkauft. So sah ich in meiner einst geliebten Heimatstadt keine berufliche Zukunft mehr. Ich nahm das Angebot einer namhaften internationalen Schiffsklassifikationsgesellschaft als Surveyor an, denn eigentlich war dies schon immer mein Traumberuf.
Ich verließ Bremen für immer.
Jetzt, während ich den Bericht schreibe, haben wir das Jahr 2013. Zwischenzeitlich ist Bremen in fast allen relevanten Bereichen auf den letzten Platz abgerutscht. Egal ob bei den Arbeitslosen, den Schulden, der Kriminalität oder der Pisastudie. Das erinnert mich an Krupp-Atlas. Die zu lasche Politik sollte mal ein bischen die Zügel anziehen und die Bürger zu mehr Flexibilität und Leistung anspornen, ohne dass die Demokratie darunter leidet. Ich habe das bei der Seefahrt unter widrigen Umständen auch geschafft.
Nach dem Aus von Krupp-Atlas wurden dessen Produkte von anderen Krupp-Tochterunternehmen übernommen. Die Kalksandstein- und Betonsteinpressen gingen zu Polysius in Beckum, die Meerwasserentsalzungsanlagen zu (mir unbekannt) und der Behälterbau zu Krupp-Rheinhausen in Duisburg.
Später erfuhr ich, dass der neue Speisewasserbehälter für Biblis A von Krupp in Rheinhausen gebaut wurde.
Heute steht auf dem ehemaligen Atlas-Gelände eine supermoderne Fabrik mit Hochregallager des Cornflakeherstellers "KELLOGS".
Herr Dr. Ing. Günther Czichon, der letzte Direktor von Krupp-Atlas in Bremen, übersandte mir freundlicherweise seine Chronologie, wie er aus seiner Sicht den Zerfall des Werkes aufgezeichnet hat. Allerdings teile ich in vielen Details seine Meinung nicht. Kaufmännisch vielleicht ja – technisch und personell nein.
. . . und zum Schluss noch eine Frage an ehemalige Atlas-Kollegen: hat noch jemand Bilder und/oder Beiträge aus damaliger Zeit, die er mir zur Ergänzung dieses Berichtes zur Verfügung stellen kann? Ich, unsere Kinder und unsere Enkelkinder würden sich sehr darüber freuen.
➧ 
➧ 
➧ 
➧ 
➧ 
➧ 
letztes Update 15. Oktober 2013
webdesign und © hrs, Casares 2008-2013